Finite Capacity Planning: Techniques for Leveraging Finite Resources
Understanding finite capacity planning is the key to successful operations management.
This article discusses why finite capacity planning is so important for manufacturing industries. Keep reading to find out how to identify capacity gaps, build comprehensive plans, and adjust your practices to achieve efficient operations.
To learn more about capacity planning and its implementation in a professional services context, read our Guide to Capacity Planning.
Key Takeaways
- Finite capacity planning is a strategic process that involves scheduling and allocating resources while accounting for constraints and limited availability.
- The benefits of this process are maximized output, minimized waste, and enhanced operational efficiency and profitability.
- Different techniques can be applied to leverage finite capacity planning, including Load Leveling, Finite Loading, Advanced Planning and Scheduling (APS), and Theory of Constraints (TOC).
- Implementing and creating a finite capacity plan includes detailed resource assessments, capacity gap management, market and customer demand research, as well as continuous monitoring and reviewing.
What Is Finite Capacity Planning?
Finite capacity planning is a strategic scheduling and resource allocation process that considers resource constraints in the production process. This differentiates the approach from material requirement planning (MRP) or infinite capacity scheduling, where a production plan has a fixed lead time that assumes infinite resource capacity.
Acknowledging the fact that the capacity of certain resources is limited means that a manufacturing firm would not accept all demand and would be willing to reject some if the product cannot be delivered at the requested time without hurting the overall profitability of the firm. This strongly contrasts the approach of MRP-based systems, which accept all the demand and try to complete the work-orders with minimum cost and delay.
Source: Finite-capacity scheduling-based planning for revenue-based capacity management
By considering capacity constraints, finite capacity planning helps organizations avoid capacity bottlenecks that can lead to inefficiencies and lost opportunities. It ensures that resources are utilized to their full potential, which helps maximize output and minimize waste.
Learn more about the main types of capacity requirement planning and why it’s important.
Why Is Finite Scheduling Important for Advanced Planning?
In the upcoming years, manufacturers are expected to face various challenges, from economic uncertainty and the shortage of skilled labor to supply chain disruptions. As a result, as many as 86% of manufacturing executives believe that smart factory solutions will drive competitiveness (Deloitte).
Finite capacity planning is a modern strategy that resolves many of the issues connected with the more traditional MRP approach.
These include:
- Failing to account for capacity resource planning constraints
- Ignoring the sequence dependence of the setup times
- Not considering the dependent nature of demand at different levels for lot-sizing procedures (procedures that are used to calculate procurement quantities)
- Assuming that job setup time, queue time, operation time, etc. are uniformly distributed
Source: A finite capacity material requirements planning system
By aligning production schedules with actual capacity, you decrease the risk of under or overprovisioning. This in turn reduces the chance of wasted resources or bottlenecks, contributing to improved customer service and increased revenue.
Additionally, good finite capacity scheduling means having more control over your production capacity in relation to current and future market trends. This builds company resilience, helping businesses withstand various external challenges.
How Do You Develop a Capacity Strategy for Production Scheduling?
When formulating a capacity strategy for finite capacity planning, consider the following steps:
- Assessing your current resource capacity
- Developing and implementing a capacity plan that takes into account your resource requirements and infrastructure
- Identifying and addressing capacity gaps and bottleneck
- Utilizing various techniques that support finite capacity scheduling
- Reviewing and iterating to ensure the plan continues to align with business objectives
We’ll discuss each in more detail in the following sections of the article.
How To Create a Finite Capacity Plan
To develop a finite capacity plan, you must first understand your organization’s production capabilities and resource availability. Accurate data collection and analysis are key elements of this process.
In professional services, capacity managers would consider employee skillsets, available time, estimated billable hours, project deadlines, and priorities in order to create a capacity plan. Professional services time tracking software can be incredibly helpful here, giving you detailed insights into how your resources are being used and keeping you on top of project timelines.
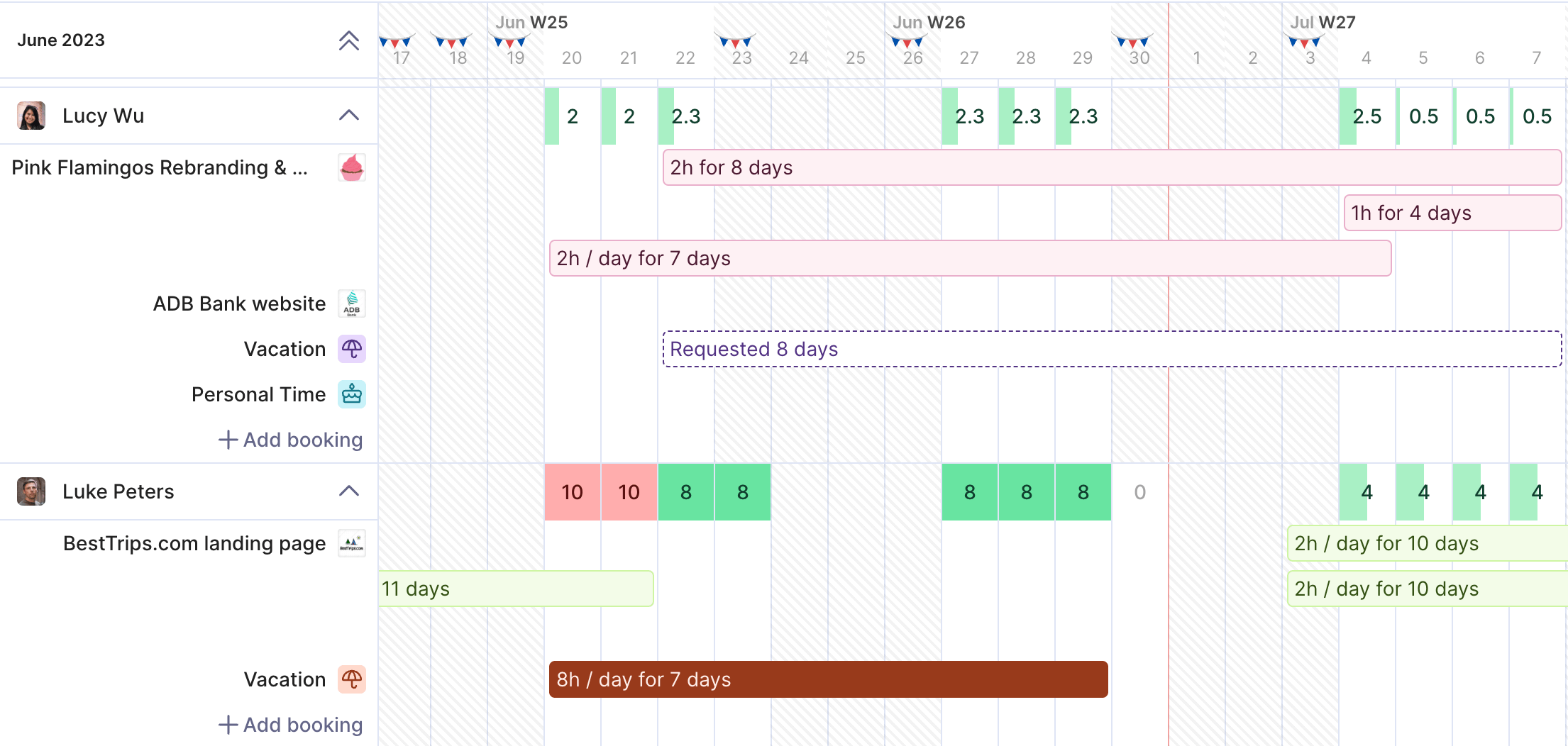
A RESOURCE PLAN CREATED WITH PRODUCTIVE, one of the best AGENCY MANAGEMENT SOFTWARE options
In the context of production-based companies, the factors that need to be assessed are: start and finish dates of operations, estimation of completion dates of orders for delivery to customers, and prediction of job arrivals and queue lengths.
Taking into account labor, equipment, materials, and all associated questions above, a production manager would use advanced capacity planning software in order to generate a realistic plan. These types of tools streamline continuous monitoring and adjustments, both of which are crucial for ensuring that your capacity plan remains relevant and effective.
Measuring capacity planning effectiveness with key capacity planning metrics is crucial, especially in finite environments.
Developing a finite capacity plan is a dynamic process that requires a mix of strategic thinking, timely iteration, and careful execution, all of which can be simplified with the right software solution.
What Are the Different Types of Finite Capacity Planning?
We can differentiate between four primary types of finite capacity planning:
- Load leveling method: This method balances production according to manufacturing facility capacity in order to maintain a stable supply. It aims to meet customer demand by keeping to a realistic schedule, delivery dates, and appropriate inventory quantities.
- Finite loading method: In comparison to level loading, finite loading goes more in-depth into the specifics of each resource, such as machine capacity, labor availability, and material constraints. It’s utilized in order to prevent the overloading of plant capacity limits. It’s usually supported by efficient production schedules, usually developed by utilizing advanced scheduling software.
- Advanced planning and scheduling (APS) method: APS systems employ advanced algorithms for the creation of production schedules that consider a facility’s finite capacity. Concepts that are usually leveraged by such software are linear and constraint-based programming, as well as heuristics and scenario planning.
- Theory of constraints (TOC) method: TOC considers particular bottlenecks in order to maximize utilization. For example, “if that constraint happens to be a particular machine, then the master schedule is developed to maximize profits given the time available on the bottleneck machine” (Encyclopedia of Production and Manufacturing Management).
Unlock Your Operational Efficiency
Switch from multiple tools and spreadsheets to an all-in-one tool that handles everything from team collaboration to advanced capacity planning.
How Do You Identify Capacity Gaps in Finite Capacity Planning?
Capacity gaps refer to the difference between the capacity of resources available and the demand required. They can be pinpointed and addressed by considering a series of questions that are relevant to your production plans and manufacturing facility processes.
Some key considerations for efficient capacity gap management are:
1. Estimation of available capacity: Ask questions about theoretical available capacity, individual and combined capacities of machines in various work centers, the scheduling constraints, historical data about breakdowns, etc.
2. Bottleneck identification and management: Since bottlenecks cause work disruption, it’s necessary to identify them by monitoring their cause and movements, as well as developing efficient strategies to manage them, such as subcontracting or adapting your internal processes.
3. Simulation models of production facility: Creating an accurate model that mimics your production setting is key to testing various capacity planning tactics. To give an example from professional services, the all-in-one project management agency software Productive provides placeholders that can be used to simulate future staffing.
Now we’re able to now see out into the future—far more than we were ever able to see before.
Read the full story: How 4Site Interactive Studios Stays Profitable Serving Non-Profits
4. Priority calculation and management: In order to optimize your manufacturing operations, you need to be able to load and execute jobs according to their priorities. Therefore, make sure to reconsider the criteria for your finite scheduling and whether the established priorities are being maintained.
5. Throughput optimization: Throughput is closely linked to bottlenecks. The main question to consider is whether you’re maintaining sufficient safety stocks to address potential material constraints and ensure stability in both inventory levels and production lines.
Source: Finite capacity planning in manufacturing systems
How Do You Implement a Finite Capacity Plan?
Once you’ve established your resource availability, as well as potential capacity gaps and bottlenecks, the next step is implementing a capacity plan.
This is done through using specific tools and techniques for finite capacity scheduling. Progress tracking is usually done with the support of advanced software tools, such as scheduling software, that can deliver real-time data and scenario planning for easier iteration.
According to Plex’s survey, more than 50% of global manufacturers utilize cloud software, and as many as 41% are increasing their cloud technology spending. When it comes to barriers to adoption, the biggest challenges are cost and technology paralysis, or being unable to decide between multiple solutions on the market. Despite this, almost half of the respondents believe that there is a need to accelerate digital transformation in order to respond to the push for higher quality (check our guide on infrastructure capacity planning to learn more).
The success of your capacity plan will hinge on your organization’s ability to anticipate hurdles and quickly respond to potential disruptions. For all of this, investing in the right ERP for professional services is key.
How Do You Monitor and Adjust Your Finite Capacity Plan?
One of the primary factors to take into account when engaging in finite capacity planning is the continuous monitoring of market trends and customer demand.
Some of the external influences that might cause changes to your capacity plan include:
- Competition: Demand for products can be significantly impacted by competitors on the market, making it key for any business to keep a close eye on the newcomers or developments in the industry.
- Seasonality: Certain products peak in demand during specific times of the year. For example, an ice cream plant should plan to produce more supply during the summer months and scale down production during winter.
- Special events: Various holidays or cyclical events can impact product demand, such as Valentine’s Day, Mother’s Day, or Black Friday.
- Economic changes: Perhaps the most difficult factor to adjust for, economic changes affect buying habits and behaviors, necessitating adjustments in your production strategies.
To summarize, considering potential disruptions to your production processes is key to maintaining efficient production plans. In volatile times, consider navigating external challenges by seeking out alternative data sets, as well as local knowledge. Then, consider ensemble modeling, or building your estimates from various, simple sources.
Under uncertain, dynamic conditions, blending many simple models often works better than using one complex model, which may be more brittle under these conditions.
Source: Harvard Business Review
Finally, don’t forget to apply continuous testing and reviewing to ensure that your strategy is up-to-date.
What Are the Best Practices for Finite Capacity Planning?
The starting point for successful capacity planning is understanding the complexities of your production facility’s capacity. This includes knowing the differences between your design capacity, effective capacity, and actual capacity.
- Design capacity is the output a production facility has in perfect conditions — or the amount of inventory that can be produced continuously, at a maximum production rate.
- Effective capacity takes into account factors such as staff and maintenance and considers various operational factors that impede maximum capacity.
- Actual capacity contains unplanned as well as planned losses, such as training for new staff or machine breakdowns.
After strategic analysis, the next essential step is maintaining a flexible mindset. As previously outlined, a facility manager needs to be able to anticipate and implement changes to their scheduling solution in order to maintain business resilience. The strategic use of technology for real-time tracking and predictive analytics can simplify these efforts.
Finally, cross-functional collaboration is important for any industry, and manufacturing is no exception. Tools that can help you track time, manage tasks, and share feedback efficiently can help you gain valuable insights and streamline your processes.
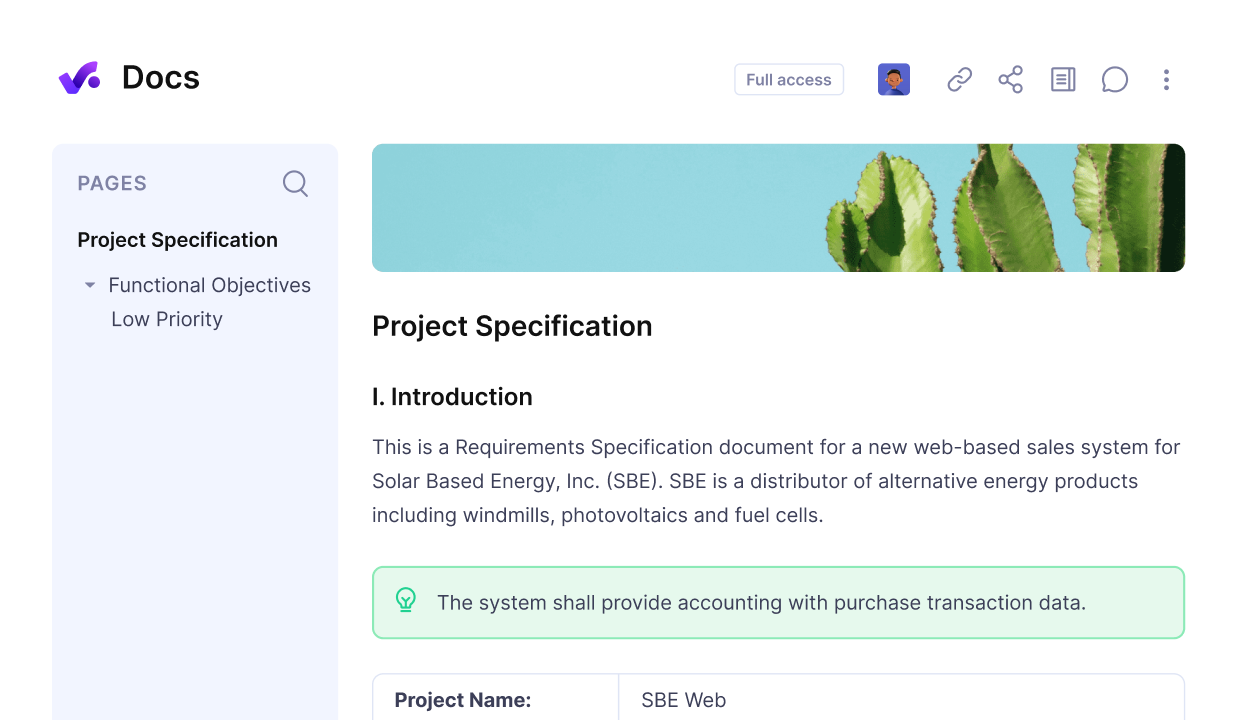
manage your tasks, share documentation, and collaborate with your teams WITH PRODUCTIVE
What Are the Challenges of Finite Capacity Planning?
The biggest challenge of finite capacity planning is being able to forecast future demand accurately. Although this is easier in a facility with a repetitive production process, finite capacity planning might be difficult to achieve in a dynamic production environment.
Inaccurate planning might lead to various issues, including capacity constraints and fulfillment issues. This can result in difficulties with satisfying demand, which ultimately impacts brand image and company revenue. However, infinite capacity planning can be just as risky by inflating inventory levels, wasting resources, and causing inefficient workflows.
In the end, the challenges of finite capacity planning can be addressed by maintaining both a strategic and flexible mindset. This means focusing on monitoring your performance while being open to adjustments in order to ensure that you’re on the right track.
Takeaway: Leveraging Finite Capacity for Operational Efficiency
Finite capacity planning is a crucial process in production management. It supports the optimal use of resources by identifying capacity gaps and ensuring that production plans reflect market demands. This, in turn, supports efficient operations and improved financial management.
Finite capacity planning can be a complex process. Forecasting customer needs isn’t always simple, especially during volatile time periods. However, by implementing best practices and techniques, as well as remaining open to iteration, production managers can get the most out of their finite capacity plans.
FAQ
What Is the Difference Between Finite and Infinite Capacity Planning?
Finite capacity planning takes into account actual capacity constraints and schedules work based on resource availability. On the other hand, infinite capacity planning assumes unlimited resource capacity and plans production without considering potential constraints or disruptions.
What Are the Advantages of Finite Capacity Planning?
Finite capacity planning can help you create a more realistic production schedule. It can minimize bottlenecks, improve resource utilization, and ensure that your business is more resilient to internal and external changes.
What Is Infinite Capacity in MRP (Material Requirements Planning)?
Infinite capacity planning assumes that there is always enough capacity available to process work at any given time. This approach deals with raw materials only, without assessing the specifics of a facility’s capacity and potential bottlenecks in the process.
What Is the Infinite Capacity Model?
The infinite capacity model is the opposite of finite scheduling. It’s a planning approach that does not consider limitations in capacity when scheduling production but instead assumes unlimited resources.
What Are the Different Types of Capacity Planning?
There are three main types of capacity planning, including workforce capacity planning (ensuring you have enough workers), product capacity planning (ensuring that you have enough inventory), and tool capacity planning (ensuring that you have enough tools to deliver services).
What Is the Difference Between Finite vs. Infinite Planning?
Finite planning acknowledges, identifies, and accommodates resource constraints, while infinite planning means scheduling production under the assumption that resources are infinite.
What Are the Disadvantages of Capacity Planning?
Capacity planning can be time-consuming and complex. It requires accurate data for effective forecasting and can be costly if future needs are miscalculated.
Why Does Capacity Planning Use Infinite Rather Than Finite Planning?
Finite planning doesn’t require detailed insights into the specifics of your resources. It’s a simpler approach compared to finite planning, which can be complex and resource-intensive to maintain.
What Is the Difference Between Capacity Planning and Resource Planning?
Capacity planning focuses on the ability to meet demand by adjusting the overall production capacity, while resource planning involves allocating resources effectively to meet production schedules within the constraints of the available capacity. Both are part of the same production planning process.
Connect With Agency Peers
Access agency-related Slack channels, exchange business insights, and join in on members-only live sessions.
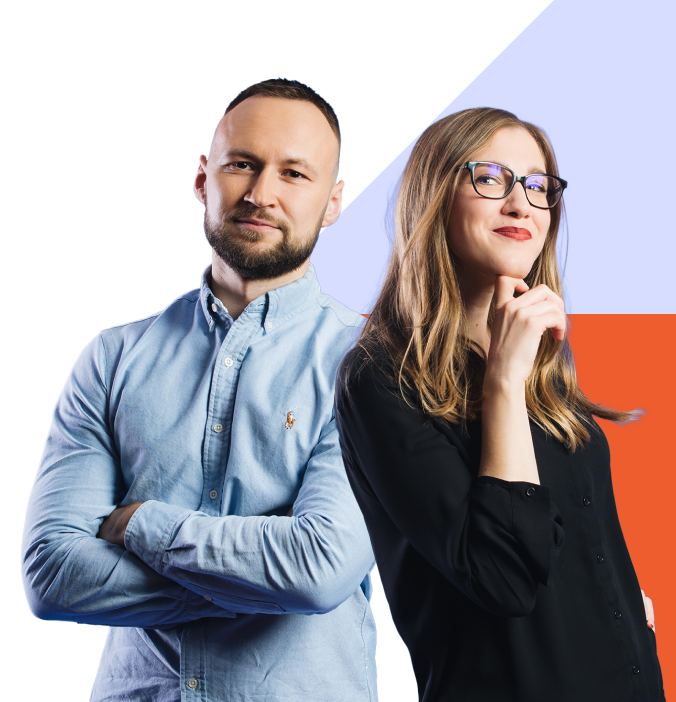