Six Sigma in Project Management for Beginners
Black Belts who? Despite some confusing terminology, Six Sigma doesn’t have to be complicated. In this article, we’ll explain in simple terms the main principles and reasons behind implementing Six Sigma in project management.
Key Takeaways
- Six Sigma is a data-driven approach which uses statistical tools and analysis to drive process improvements and reduce defects
- Customer feedback and strong customer relations are at the core of Six Sigma’s principles
- The main methodology used is DMAIC, which includes five distinct stages: Define, Measure, Analyze, Improve, Control
- Six Sigma also prescribes core organizational roles, such as Green Belts, Black Belts, and Master Black Belts, which ensure successful implementation
What Is Six Sigma in Project Management?
Six Sigma is a data-driven approach for business management. It’s main focus is on driving process improvement based on the voice of the customer (VOC).
Its main principle is to achieve a nearly flawless level of performance, with a maximum of 3.4 defects per million opportunities (DPMO).
How do project professionals achieve this? By conducting rigorous data analysis on how different inputs and variations change the outcomes of processes.
By analyzing different possibilities, businesses can come up with the best possible combination (with the least variation) to achieve their project parameters.
Origins and History of Six Sigma
Six Sigma was originated at Motorola in the mid-1980s. The company was struggling with its brand image and customer satisfaction; the executive team took cues from Japanese professionals to develop a new methodology and resolve these issues.
It was a huge success. In Demystifying Six Sigma, A. Larsons reports the results:
- Cost of sales were reduced by 30% within manufacturing operations
- Cycle times and cost were reduced by as much as 90% within administrative and service functions
Nowadays, Six Sigma is applied with the same purpose of reducing costs and optimizing operations, mainly in larger businesses (learn more about data-driven project budget control).
Core Principles of Six Sigma in Project Management
The basic principles of Six Sigma include:
- Six Sigma’s main goal is improving business processes; its key strategies include the design, optimization, and validation of processes
- Six Sigma is focused on the voice of the customer; all processes and improvements are based on what the customer wants, needs, and is willing to buy
- A focus on tangible return on investment and increasing business profit margin; monitoring key performance indicators is one of the basics of Six Sigma
- Leadership and management buy-in, as well as understanding on the entire company level is necessary for successful implementation
- For Six Sigma to succeed, you need to have connected business metrics that are readily accessible and visible to all relevant
Six Sigma is based on continuous improvement. Unlike the waterfall project management methodology, its purpose is to implement incremental improvements, even if this means going to previous stages in your processes.
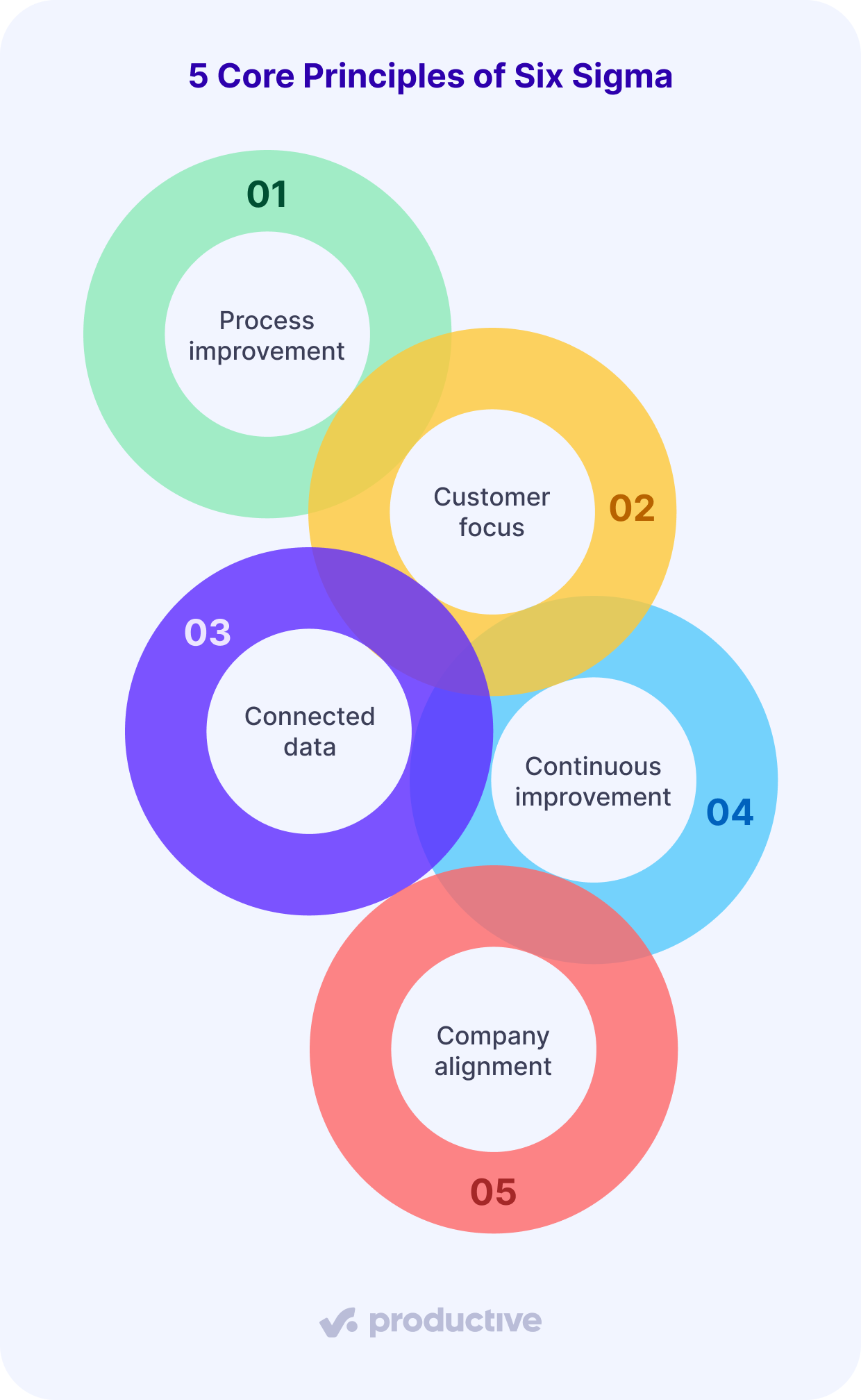
DMAIC Six Sigma Methodology
The DMAIC methodology is a core component of Six Sigma. It’s considered as a traditional strategy, and offers a structured approach to process improvement that can be applied to various project management scenarios.
Let’s take a closer look at each of the five phases: Define, Measure, Analyze, Improve, and Control.
Define
Defining projects is about truly understanding what your problem areas are, and creating a no-nonsense path to resolving it. The main steps of the Define stage include:
- Defining the problem and goals (making sure they’re clear and attainable)
- Setting the scope of the project
- Identifying the customer requirements and needs
- Determining roles and responsibilities within teams
- Process mapping – setting benchmarks, techniques, etc.
Measure
In the Measure phase, the project team needs to define effective solutions for how they’ll measure their success. This includes:
- The type of data that needs to be gathered
- How the data will be gathered
- Which analysis methods will be used
- How the data will be visualized
This usually also includes the implementation of software solutions that can help gather and analyze this data: Excel is the basic option, while more advanced project management software can be another good option.
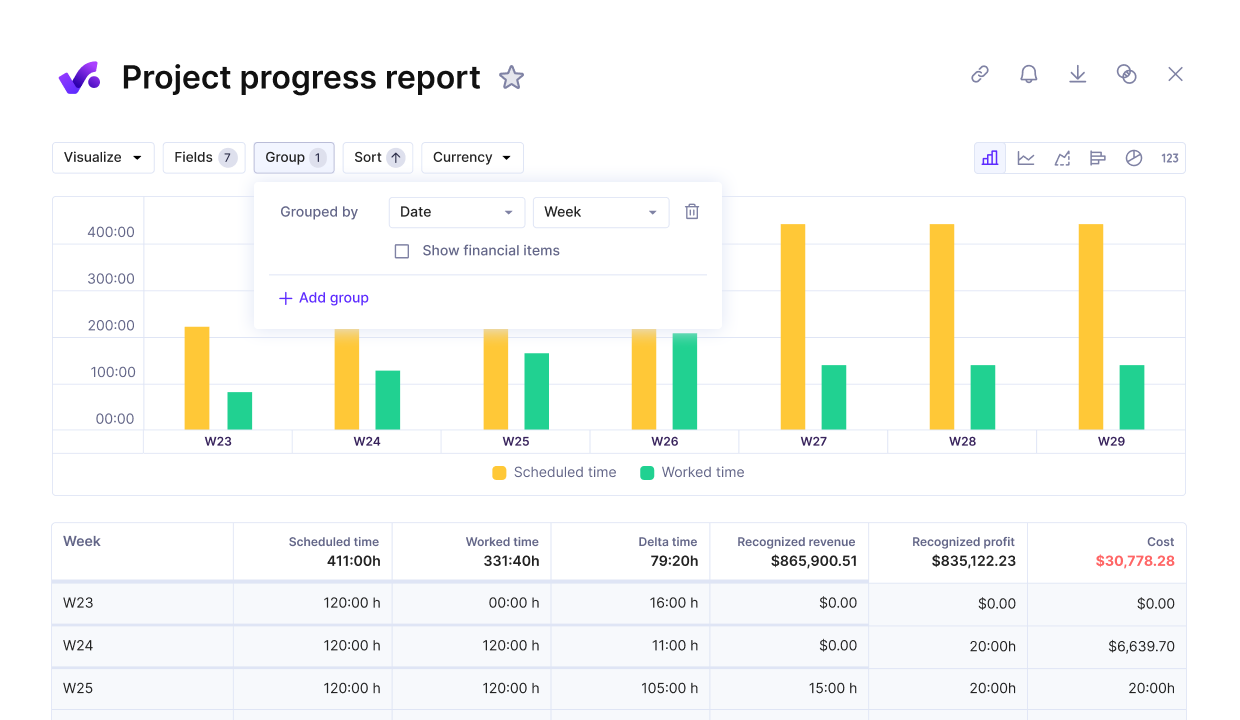
Productive provides a consolidated view of business metrics
Analyze
An important aspect of the Analyze stage is to consider whether the data collection phase was effective—if not, going back and improving this step can also be considered an important part of your business strategy.
At the end of the analyze stage, you’ll want to have answers to the following questions:
- What was the area that needed improvement?
- How was the data examined to understand the issue?
- What were the main causes leading to this problem?
- How was the data used to find patterns or inconsistencies?
- Did the analysis lead to any changes in the problem or its focus?
Improve
In the Improve stage, you’ll be ready to use the insights generated so far to develop potential solutions. The most important processes of the improve stage are brainstorming sessions and the Design of Experiments (DOE) methodology, though the latter has roots in manufacturing and is often difficult to apply in other industries.
Piloting new solutions in controlled environments is essential to assess their effectiveness before full-scale implementation—it ensures that improvements are sustainable and align with project goals.
Control
The final phase of the DMAIC methodology is all about monitoring and standardizing the processes developed as part of the previous stages. It guarantees that improvements are maintained and the process remains stable.
Control involves:
- Establishing KPIs and control charts to monitor process performance
- Defining who is resposible for monitoring and reporting success
- Revising existing documentation to reflect quality improvements
- Developing project plans for how to react to potential roadblocks
Six Sigma Methodologies Explained
Apart from DMAIC, which is a traditional Six Sigma methodology, there are some other ones which are frequently mentioned.
One of them is DCOV (Design, Characterize, Analyze, Verify), which is a proactive approach that’s focused on preventing problems from occuring in the first place.
Another is DMADV (Define, Measure, Analyze, Define, Verify), which is focused on developing new processes, instead of refining existing ones.
In comparison, DMAIC is more of a reactive approach, which focuses on identifying and fixing a problem in current processes.
These different methodologies have varying applications. Each methodology ensures quality and efficiency, but the choice depends on whether the focus is on improvement, prevention, or innovation.
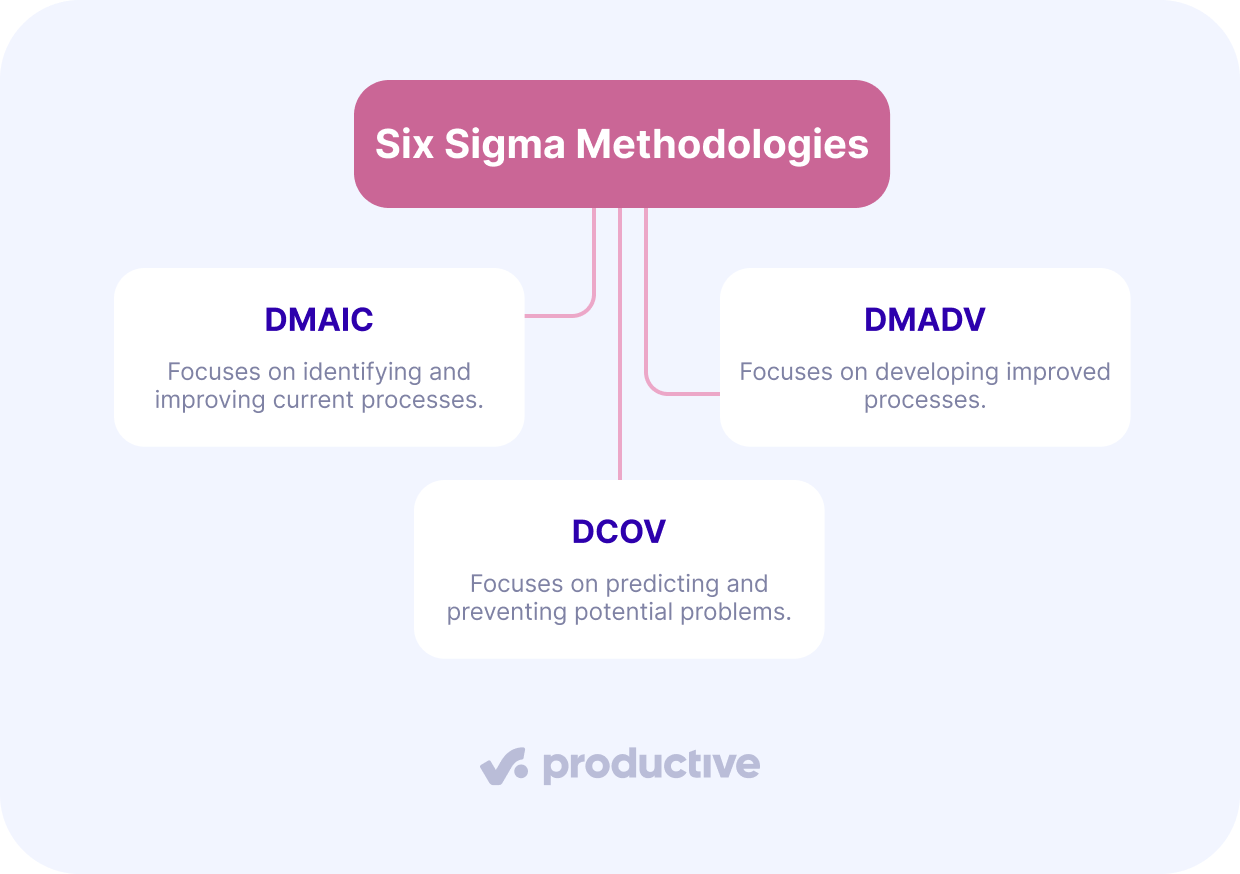
What Is Lean Six Sigma?
Lean Six Sigma is a hybrid approach that combines the main characteristics of Lean project management and Six Sigma project management.
It combines the quality management focus of Six Sigma with the efficiency principles of Lean management. Putting it simply, it’s a way to make work better and faster at the same time.
Here’s another way of describing Lean Six Sigma:
- Six Sigma focuses on fixing individual business processes; it helps improve the value-adding steps of your project process
- Lean focuses on making the connections (or workflows) between these processes better; it focuses of eliminating or streamlining non-value-adding processes
Both of these methodologies work together in order to ensure sustainable operations and growth and improve profit margins.
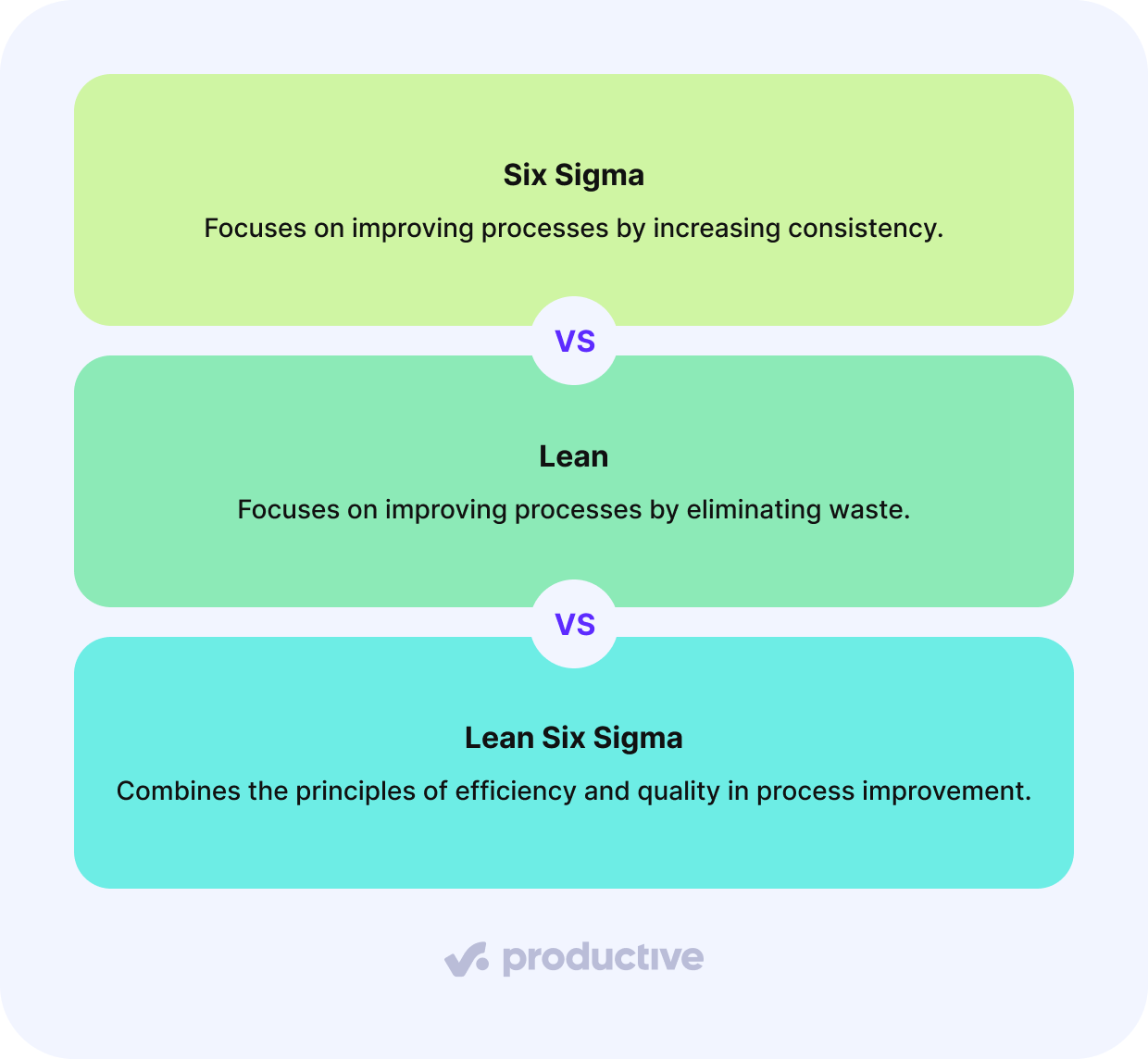
Benefits of Six Sigma
Six Sigma offers numerous benefits that make it a powerful methodology for improving business processes and achieving operational efficiency.
One of its most significant advantages is its focus on data-driven decision-making, ensuring that improvements are based on measurable insights rather than guesswork.
By minimizing process variability and reducing defects, Six Sigma enhances product and service quality, leading to increased customer satisfaction and loyalty.
Another key benefit is cost reduction. By identifying inefficiencies and eliminating waste, organizations can significantly lower operational expenses while increasing profitability.
Six Sigma also improves productivity by streamlining workflows and optimizing resource utilization, allowing employees to focus on high-value tasks rather than fixing recurring problems.
The methodology promotes a culture of continuous improvement, where teams are encouraged to proactively seek enhancements rather than react to issues after they occur.
Real-Life Examples of Businesses Using Six Sigma
Here are some popular examples of businesses that have achieved tangible benefits by using Six Sigma project management:
- General Electric profited between $7 to $10 billion from Six Sigma in 5 years
- Dupont added $1 billion to its bottomline within 2 years of initiating its Six Sigma program
- Honeywell saved more than $2 billion in direct costs and achieved record margins
- Bank of America cut cycle times by more than 50% within 3 years
Source: C. Gygi, N. DeCarlo, and B. Williams in Six Sigma for Dummies
Cons of Six Sigma
While Six Sigma offers impressive benefits, it is not without its challenges.
One of the biggest drawbacks is that it requires full organizational buy-in, from executives to employees, which can be difficult to achieve. Without widespread commitment, implementation efforts may fail or lose momentum.
Additionally, Six Sigma is time-consuming and resource-intensive, demanding extensive training, certification, and ongoing commitment.
Organizations must invest in expert personnel like Black Belts and Master Black Belts, leading to high costs that may not be feasible for smaller businesses.
Another limitation is its rigid structure, which may not suit industries that require flexibility and rapid adaptability.
While it is highly effective in manufacturing and process-driven industries, its structured approach may not be the best fit for creative or fast-changing environments.
Which Businesses is Six Sigma For?
Six Sigma is most often implemented in larger businesses, as they have the resources to invest in training, certification, and process improvement initiatives.
However, smaller businesses can also benefit from Six Sigma’s statistical approach and customer focus, particularly in managing complex projects.
While widely used in manufacturing to reduce defects and process variations, Six Sigma is also applied in industries such as:
- Healthcare, to improve patient care and reduce errors
- Finance and banking, to enhance risk management and service quality
- Supply chain and logistics, to optimize inventory and reduce delays
- Service-based industries, to improve operational efficiency and customer satisfaction
Six Sigma Certification Levels
Six Sigma follows a structured hierarchy of certification levels, each with distinct responsibilities to drive continuous improvement. The terminology can vary depending on the resources.
For example, A. Larson defines two levels of certification in Demystifying Six Sigma: the black belts and the green belts.
The green belts have the basic necessary formal training necessary, while the black belts have advanced training based on their aptitude for team management and leadership.
On the other hand, D.H. Stamatis, in Six Sigma Fundamentals, defines four main roles under Six Sigma:
- Green Belts support projects, handle detailed tasks, and work under guidance.
- Black Belts lead projects independently, solve problems, and build credibility.
- Master Black Belts mentor others, drive leadership, and represent the organization.
- Executives and Champions provide vision, influence decisions, allocate resources, and shape strategy for long-term success.
Additional Sigma certification levels can also be adopted for project manager beginners that are under green belts, called white belts and yellow belts.
Tools and Implementation of Six Sigma in Project Management
Successfully implementing Six Sigma in project management requires a combination of structured methodologies, statistical tools, and data-driven decision-making.
By leveraging key analytical tools and techniques, organizations can enhance process efficiency, reduce defects, and improve overall quality.
Process Mapping
Process mapping in Six Sigma is a visual representation of a workflow, detailing each step, input, and output. It helps identify inefficiencies, bottlenecks, and variations, enabling data-driven improvements. Common types include SIPOC, value stream maps, and flowcharts.
Six Sigma Project Metrics
Tracking metrics in Six Sigma projects is essential for evaluating the effectiveness of quality improvement initiatives and ensuring that implemented solutions deliver the desired results.
Key performance indicators (KPIs) such as defect rates, cycle time, and process capability indices (Cpk) provide valuable insights into the project’s progress and impact.
The DMAIC framework offers a structured approach for measuring and analyzing these metrics, with a focus on establishing baseline data during the Measure phase.
Control charts are utilized to monitor process stability over time. Variance analysis further helps in identifying fluctuations from expected performance.
Consider the following key points when tracking Six Sigma project metrics:
- Establish clear and measurable KPIs aligned with project goals
- Collect accurate and reliable data throughout the project lifecycle
- Utilize statistical tools to analyze data and identify trends or patterns
Statistical & Data Analysis Techniques
A key aspect of Six Sigma is using Statistical Process Control (SPC) and data analysis techniques to monitor and improve process performance.
Control charts track variations over time, distinguishing between common cause and special cause variations.
Another essential tool is process capability analysis, which assesses whether processes meet customer specifications and highlights areas for improvement.
In addition, Six Sigma relies on various data analysis techniques, including Root Cause Analysis (RCA) to identify underlying issues, Failure Mode and Effects Analysis (FMEA) to assess risks and prioritize corrective actions, and Pareto analysis to focus on the most significant factors contributing to defects
Project Management Tools
Finally, project management software isn’t a crucial part of Six Sigma itself, but it is a necessary tool for project managers.
Project management tools help manage project scope and budgets, which contributes to data collection and process improvements.
There are different types of project management software depending on your industry and business size. A popular option for professional service companies is Productive, which includes project, financial, and resource management features.
Conclusion on Six Sigma
We’ve explored the basic of Six Sigma, its role in project management, methodologies, organizational structure, and applications. While it offers a data-driven approach to quality improvement and cost reduction, implementing Six Sigma isn’t without challenges. It requires significant training, resources, and cultural change.
Deliver Profitable Projects With Productive
Switch from multiple tools and spreadsheets to an all-in-one solution for professional services management.
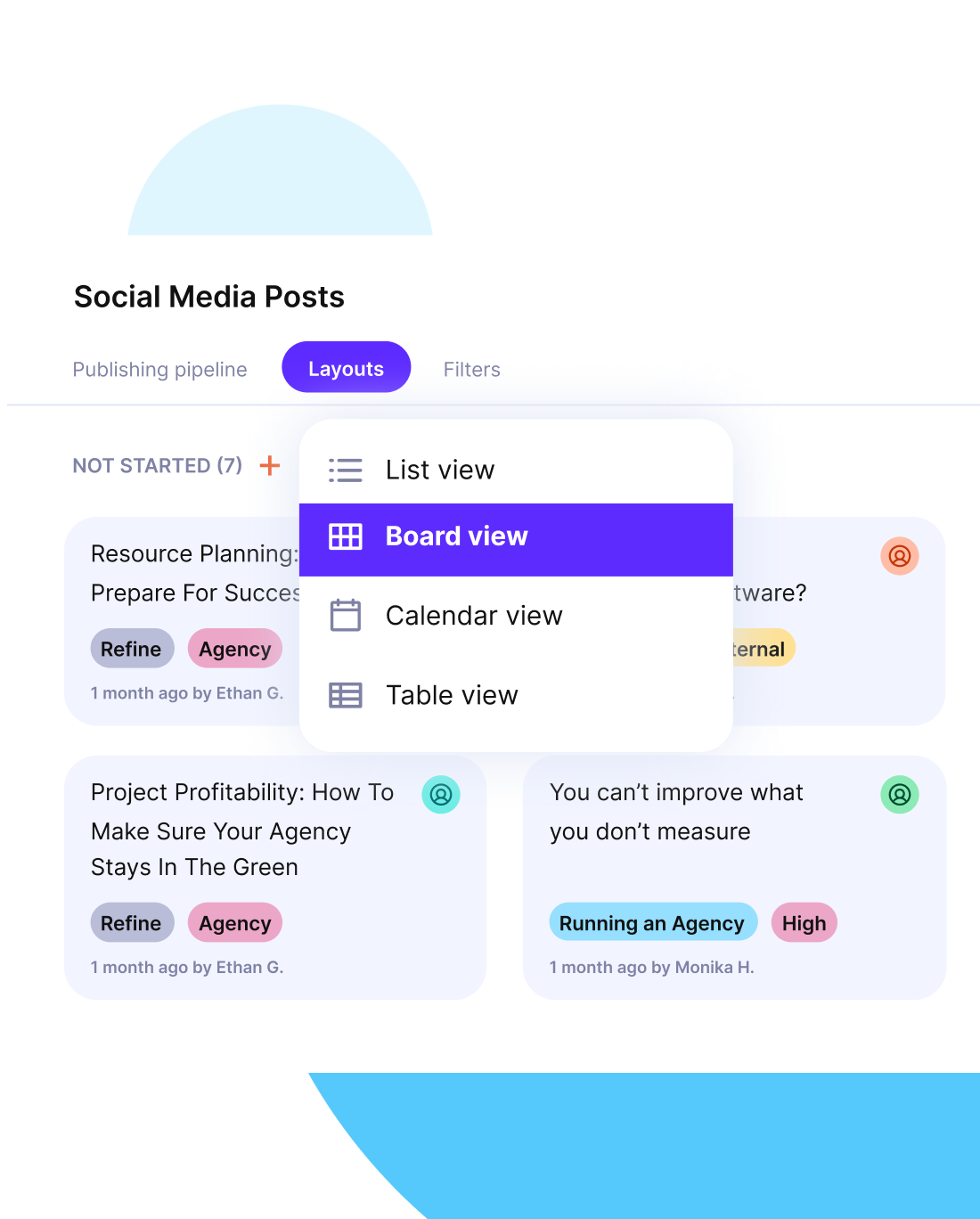