Guide to Lean Project Management
Lean project management is a method for optimizing project processes. It applies Lean principles to maximize value and minimize waste. By the end of this article, you’ll know all about Lean project management, its key principles, benefits, best practices and implementation challenges. Let’s start with the definition.
Key Takeaways:
- Lean project management focuses on maximizing customer value while minimizing waste.
- Five core principles of Lean project management: identify value, map value stream, create flow, establish pull, and pursue perfection.
- Powerful tools like value stream mapping, Kanban, and PDCA support waste reduction lean practices.
- Successful Lean implementation requires cultural transformation, ongoing training, clear metrics, and openness to experimentation and collaboration.
What Is Lean Project Management?
Lean project management is a methodology that focuses on identifying and delivering value from the customer’s perspective, streamlining processes, and continuously improving.
The goal is to eliminate waste and inefficiencies, while getting better along the way.
How Was the Lean Methodology Created?
Lean methods have their roots in the Toyota Production System (TPS) that was developed between 1948 and 1975.
Later in the 80s, Toyota’s Lean manufacturing principles of waste reduction and value maximization started to be applied in general project management and became Lean project management.
This shift from manufacturing to project management involved adopting techniques like value stream mapping to identify and eliminate inefficiencies in project workflows. Continuous improvement, or Kaizen, became a central component of of this approach, as it encourages teams to iteratively refine processes and deliver higher value to customers.
Now that you understand what Lean is, and where it came from, let’s talk about its five principles.
What Are the Five Principles of Lean Methodology?
The five principles of Lean methodology are identifying value from the customer’s perspective, mapping the value stream, creating continuous flow, establishing pull systems, and pursuing perfection.
In the next sections we’ll get break down each core principle and get into details behind the project process.
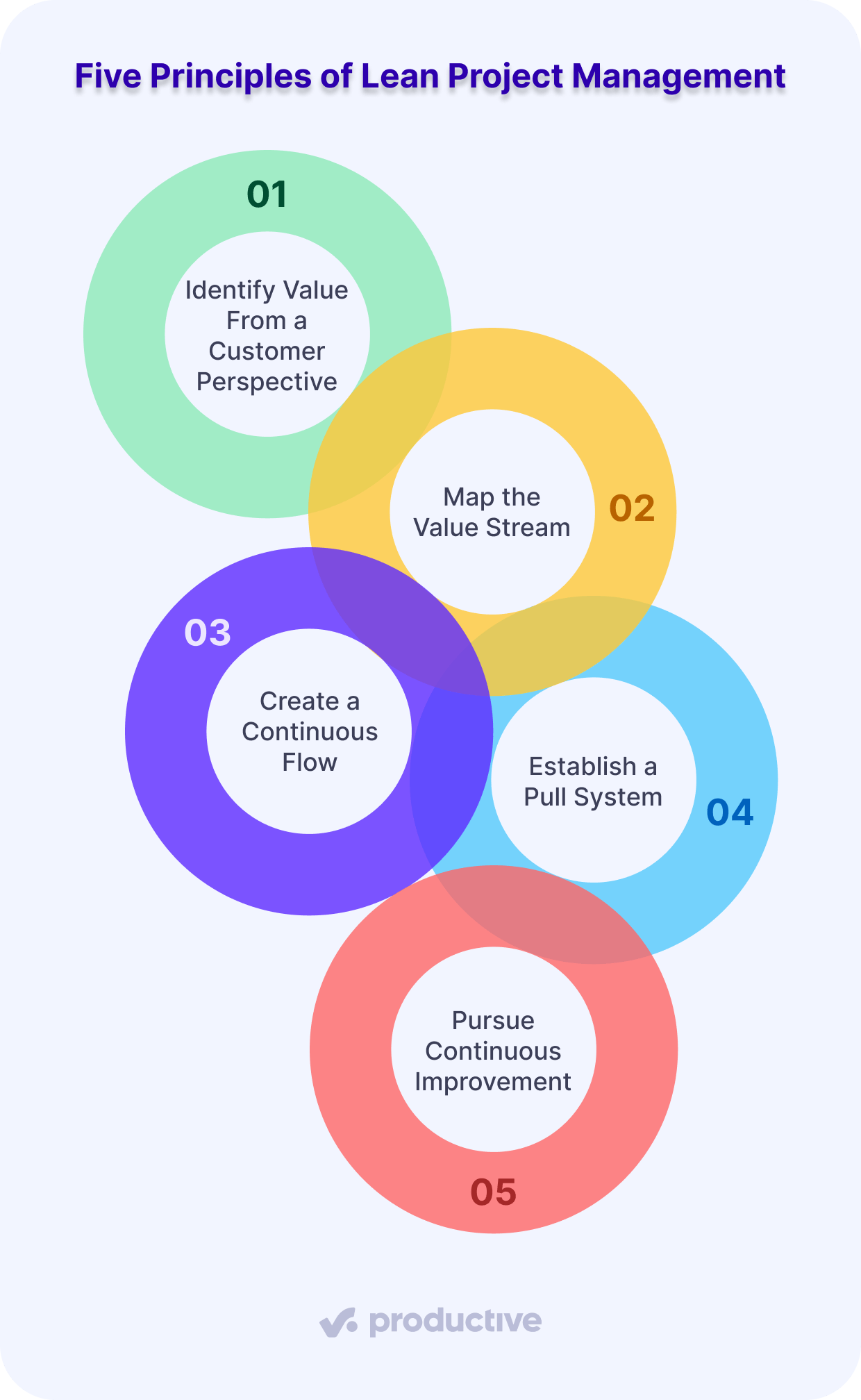
First Principle: Identify Value From a Customer Perspective
In the Lean approach, the starting point is understanding what customers truly need and desire. When project teams focus on the customer value they can:
- Effectively prioritize tasks and resources, reducing waste and minimizing the risk of project failure.
- Guarantee alignment with customer expectations so that they have satisfied customers.
- Create pull systems that initiate work only when there’s actual customer demand, preventing unnecessary accumulation of tasks and resources.
- Cultivate direct customer communication to clarify objectives, requirements, and acceptance criteria.
The goal of this principle is to create a customer-centric approach to project management processes. This healthy approach translates to more successful outcomes and enhanced customer satisfaction.
Second Principle: Map the Value Stream
To begin mapping the project value stream, you’ll need to analyze your current workflow and processes. This involves closely examining each step in the project lifecycle, from initiation to completion.
Teams need to document the actions taken, resources used, and time spent.
Analyzing Current Workflow
A value stream is a visual representation of all actions and processes in your project. The visual helps to identify value-adding and non-value-adding activities. A value stream map (VSM) help you:
- Highlight the types of waste in the current workflow
- Pinpoint areas for process improvement
- Establish a baseline for efficiency
- Set targets for enhancing the continuous flow
- Regularly update the map to reflect changes made
Third Principle: Create a Continuous Flow
The continuous flow is created by streamlined processes. While streamlining critical activities, you’ll minimize bottlenecks and guarantee smooth shifts between tasks. This, in turn, eliminates unnecessary handoffs and delays, and you increase productivity and capacity.
Implementing Pull Systems and Streamlining Process
Implementing pull systems is very helpful here. The idea behind the pull system is to initiate work only when there’s actual customer demand. That way you maintain a steady flow of tasks and reduce excess inventory waste.
More about pull systems in the next part of the artice.
Reducing Bottlenecks
Bottlenecks hamper project success. Project managers hate them because they disrupt the smooth flow of work and cause delays that impact the entire project’s timeline.
You might also want to consider employing Kanban boards to help visualize processes, manage tasks, and limit WIP.
To sum it up, the benefits of streamlined processes are:
- Elimination of waste and bottlenecks
- Guarantee of smooth, uninterrupted work and efficient processes
- More efficient project teams due to enhanced communication and coordination
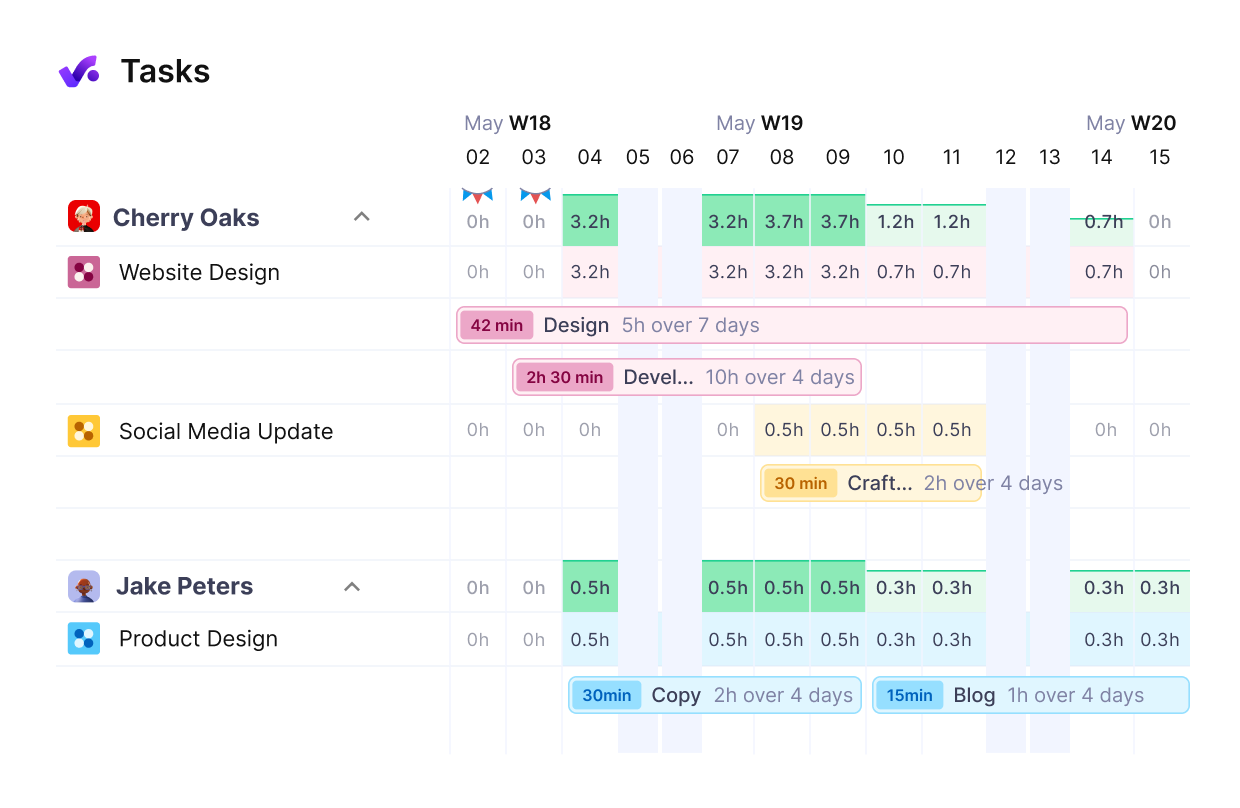
Keep your team aligned and your projects on schedule. Productive’s project management tools ensure every phase runs smoothly.
Fourth Principle: Establish a Pull System
In a pull system, you initiate work only when there’s actual customer demand, ensuring just-in-time delivery and minimizing excess inventory. This demand-driven approach contrasts with traditional push systems.
Traditionally, production is based on forecasts, which often aren’t 100% correct. As a result, the wrong input data leads to overproduction and resource wastage.
Just-in-Time Delivery
The idea behind just-in-time delivery (JIT) is that the product is ready only when it’s needed.
The pull system we previously talked about is a key component here because it initiates work only when there’s actual demand.
This way, excess inventory is reduced from the start, and project waste is minimized.
Here’s how teams benefit from just-in-time delivery:
- It’s easier to respond to changing demands
- Improved efficiency of the entire project management process
- Considerable reduction of lead times
- Utilize Kanban for visual workflow management
- Foster continuous improvement
Fifth Principle: Pursue Continuous Improvement
Kaizen (also know as continuous process improvement), means making constant incremental changes that enhance efficiency throughout the project lifecycle.
Lean project managers should regularly reassess processes and adapt to changing demands. When you constantly make little changes, they translate to improved outcomes and more successful projects.
Since this principle encourages organizations to view work systems as dynamic, they always show new opportunities for optimization.
Pursuing perfection through Kaizen leads to:
- Enhanced operational efficiency through small, incremental changes
- Reduced project waste
- Healthier collaborative culture of the entire team
- A regularly updated ongoing process that meets evolving demands
- Positive customer feedback due to consistent, high-quality results
What Are the Benefits of Lean Practices?
The benefits of Lean practices are increased efficiency, reduced waste, enhanced customer satisfaction, and improved team collaboration.
Let’s expand on each one:
Increased Efficiency
When you put lean management principles into action increased efficiency becomes apparent. This approach to project management is used in a huge variety of industries – from construction and manufacturing, to IT development and creative project management.
Real world examples speak real results. When BBC adopted Lean in its software development projects, their team achieved impressive results. As the Queen’s University in Belfast states:
The evidence shows that over the 12-month period, lead time to deliver software improved by 37%, consistency of delivery rose by 47%, and defects reported by customers fell 24%.
SOURCE: QUEEN’S UNIVERISTY BELFAST
Reduced Waste
The waste-minimization focus systematically eliminates non-value-adding activities. As a result, organizations deliver more value with the same resources and reduce project costs.
Enhanced Customer Satisfaction
this approach focuses on customer-defined value, project outcomes are aligned closely with customer requirements and expectations.
Happy customers are loyal customers. The systematic elimination of defects through continuous improvement practices enhances product quality.
Improved Team Collaboration
Collaborative tools like Kanban project management and value stream mapping help teams visualize workflows, leading to better coordination and more effective task management.
When team members are included in the planning process, they’re encouraged to take ownership and be more accountable. The practices covered in this article increase morale and collaboration across project phases.
Additionally, continuous improvement initiatives within Lean methodologies promote a culture of teamwork by encouraging regular feedback and collaborative problem-solving among team members. Excess meetings and unclear roles are also a waste.
Lean practices allow teams to focus more on value-adding activities, so the clutter of excess meetings and back-and-forth debates are also cut out.
As a result, these practices cultivate a healthy work environment that thrives on effective communication and teamwork.
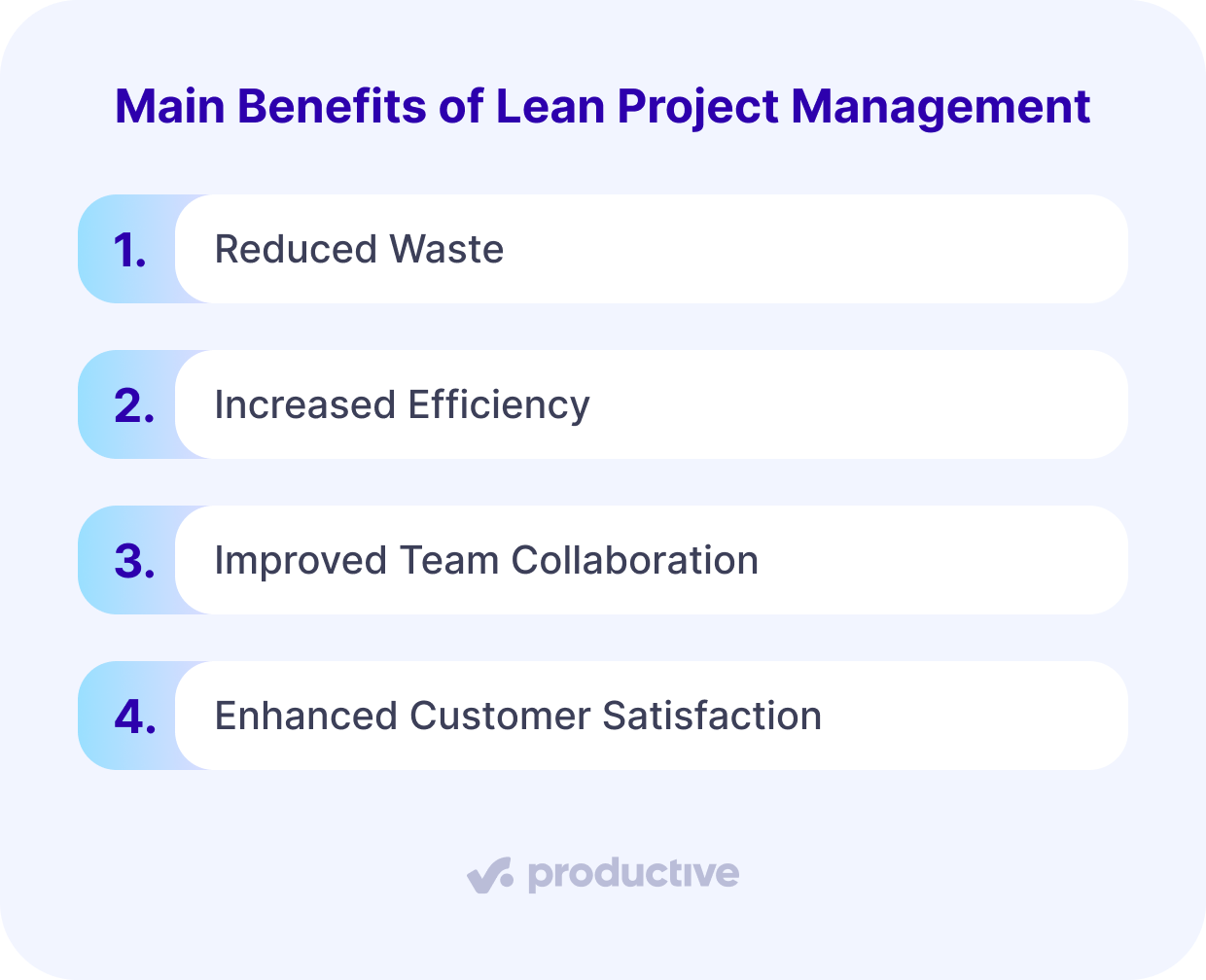
What Are Lean Project Management Tools?
Lean project management tools are the Deming Cycle, Kanban and Lean Six Sigma Techniques (part of the DMEDI framework).
All of these tools provide a structured approach to implementing changes, evaluating their effectiveness, and refining them based on the results.
Deming Cycle (PDCA)
The Deming Cycle, often referred to as the PDCA (Plan-Do-Check-Act) Cycle, is a powerful tool for continuous process improvement and optimization.
The PDCA Cycle provides a structured framework for ongoing learning and adaptation. This framework ensures that your projects remain aligned with evolving business needs and deliver maximum value to stakeholders.
The tool’s iterative approach allows you to systematically plan, implement, assess, and standardize changes to enhance project outcomes.
The goal is to follow the four phases of the cycle, so that you can:
- Set clear objectives and develop a strategy based on data analysis
- Implement planned changes on a small scale to test their impact
- Evaluate the results against expected outcomes to identify successes and areas for improvement
- Standardize successful changes and revise unsuccessful ones for further optimization
Kanban Methodology
The Kanban methodology is a powerful visual tool that supports Lean practices. The idea is to visualize work on boards that track tasks through various stages organized in columns (for example, to-do, doing, and done).
Project managers love it because their teams get real-time visibility into project status and bottlenecks. Kanban’s core principles revolve around limiting work in progress (WIP), managing flow, and making process policies explicit.
This pull-based system aligns work with actual customer demand, reducing cycle times and improving lead times.
Teams can use physical or digital Kanban boards (project management software features), which provide flexibility in tracking tasks and further improve collaboration.
Lean Six Sigma Techniques
Alongside DMAIC, Lean Six Sigma utilizes the DMEDI framework (Define, Measure, Explore, Develop, Implement) to tackle new process design or product development initiatives.
This methodology guides teams through the vital stages of identifying customer needs, brainstorming innovative solutions, and implementing the most promising concepts.
DMEDI Framework
One powerful Lean Six Sigma technique that can greatly enhance your project management efficiency is the DMEDI framework. This structured approach consists of five key phases:
- Define clear project goals and customer needs
- Measure relevant data to assess current processes
- Explore potential solutions to address issues
- Develop refined solutions
- Implement changes while monitoring outcomes for sustained improvements
How To Implement Lean Principles?
Implementing Lean principles starts with the organizational culture, mindset, and practices. You’ll also need to invest in training and development programs.
The training’s goal is to equip your team with the knowledge and skills necessary to embrace Lean principles and apply them effectively in their daily work.
Additionally, start using the right Lean project management software to streamline the implementation. Enable real-time data collection, analysis, and decision-making to drive continuous improvement throughout the entire project.
Cultural Transformation
When starting implementation journey, project managers need to recognize that a successful change involves more than just adopting new tools and techniques.
A cultural transformation is necessary, where teams embrace continuous improvement (Kaizen) as a core value.
This shift towards a Lean culture emphasizes collaboration and communication, leading to increased productivity and shared goals. Senior management support is critical in cultivating the right mindset, driving engagement and motivating teams to adopt Lean practices.
Key aspects of this cultural transformation include:
- Fostering an environment that encourages experimentation and learning from failures
- Providing regular training and education on key principles to overcome resistance to change
- Establishing clear metrics for success and regularly evaluating project performance
- Encouraging open communication and collaboration among team members
- Empowering employees to identify and eliminate waste in processes
Training and Development
As we said, a successful cultural transformation towards Lean practices relies heavily on training and development programs.
Implementing Lean principles requires ongoing education to guarantee team members understand and apply concepts effectively, overcoming resistance to change and misunderstanding.
Value stream mapping (VSM) is a powerful tool that helps teams visualize workflows, identify waste, and develop targeted improvement plans for enhanced efficiency.
Regular training sessions on Lean methodologies, like the 5S framework and Kanban systems, can notably improve workplace organization and optimize workflow management.
Certification programs, available at various belt levels, provide structured learning paths that enhance team members’ skills and validate their expertise in Lean practices.
Establishing measurable goals during training allows organizations to track progress in waste reduction and continuous improvement, reinforcing the importance of Lean principles in daily operations.
What Are the Challenges of Implementing Lean Principles?
The challenges of Lean project management are resistance to change, difficulty measuring progress, and balancing Lean practices with existing organizational culture.
Keep in mind that these implementation obstacles are pretty common.
However, by employing effective strategies like conducting value stream mapping, setting measurable goals, and fostering a supportive environment, you can overcome these challenges and pave the way for successful Lean implementation.
Continuously reviewing and refining your Lean processes will guarantee that your organization remains on the path to project success and stakeholder satisfaction.
Common Implementation Obstacles
Implementing Lean practices can present various obstacles that organizations must solve to guarantee successful adoption.
Resistance to change often stems from a lack of understanding of Lean principles, necessitating ongoing training and education for team members. Measuring progress and success in Lean initiatives can be challenging, making it essential to establish clear metrics and goals from the outset.
Misalignment of Lean practices with existing organizational culture may hinder adoption, emphasizing the importance of leadership commitment and support for a Lean mindset.
Key obstacles to watch out for include:
- Resistance to change due to unfamiliarity with Lean principles
- Difficulty measuring progress and success in Lean initiatives
- Misalignment of Lean practices with existing organizational culture
- Complexities when integrating Lean with traditional project management methodologies
- Lack of effective communication regarding customer value and project goals
To overcome these hurdles, organizations must prioritize ongoing training, set clear metrics, secure leadership buy-in, carefully plan the integration of Lean with existing processes, and maintain regular stakeholder engagement.
Strategies for Successful Adoption of Lean Principles
Overcoming the challenges associated with adopting Lean project management requires a strategic approach that addresses resistance to change, establishes clear metrics, and aligns Lean practices with organizational culture.
To guarantee successful implementation, it’s important to provide ongoing lean project management training and education for team members, enabling them to grasp the principles of Lean and embrace the necessary changes.
By conducting value stream mapping (VSM), you can identify waste and optimize workflows, making processes more efficient and easier to visualize. Setting measurable goals for waste reduction and regularly reviewing processes are fundamental for maintaining continuous improvement and guaranteeing alignment with project objectives.
Engaging senior management support is significant, as their commitment can foster a Lean culture and drive organization-wide acceptance of Lean practices. Balancing these practices with existing organizational culture is key to preventing disruptions and facilitating smoother changes.
A bonus tip for a successful implementation of Lean principles is to try out project management software like Productive. These tools help delegate and track tasks, use different project views, automate workflows, improve efficiency and so much more.
Try Productive’s project management tools
Closing Thoughts on Lean Practices
Adopting lean practices can streamline processes, reduce waste, and more efficiently deliver value to customers.
While implementing lean principles may present challenges, the benefits of increased productivity, improved quality, and enhanced customer satisfaction make it worthwhile.
If you want to succeed with lean project management, focus on continuous improvement, collaboration, and a willingness to adapt to change.
With the right mindset and tools like Productive, you can unleash your projects’ full potential. Book a demo and start today.
Connect With Agency Peers
Access agency-related Slack channels, exchange business insights, and join in on members-only live sessions.
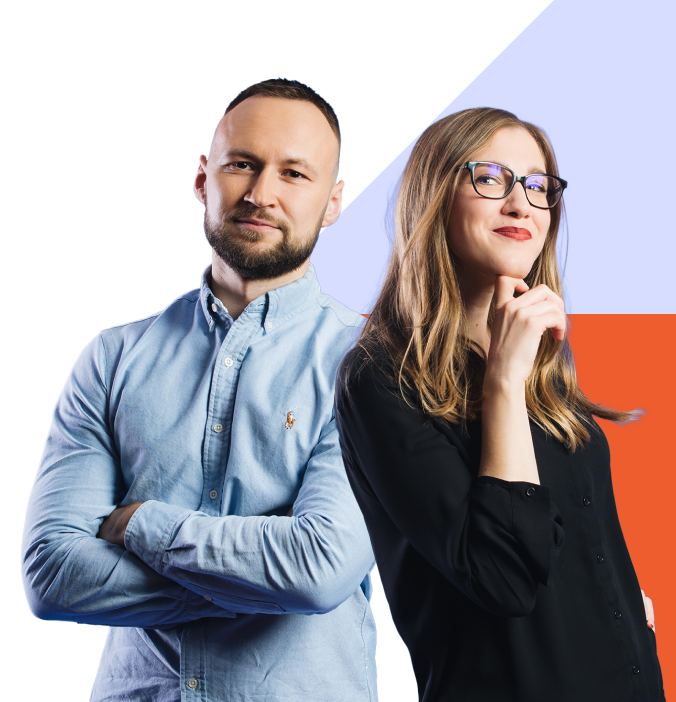